TRADITIONAL ELECTRICAL DISTRIBUTION SYSTEMS operate autonomously and lack comprehensive feedback as to the status of the energy resources available. When there is a fault it’s noticed by the lack of power and then the fault needs to be determined usually by an operator inspecting the various circuit breakers that could be affected.
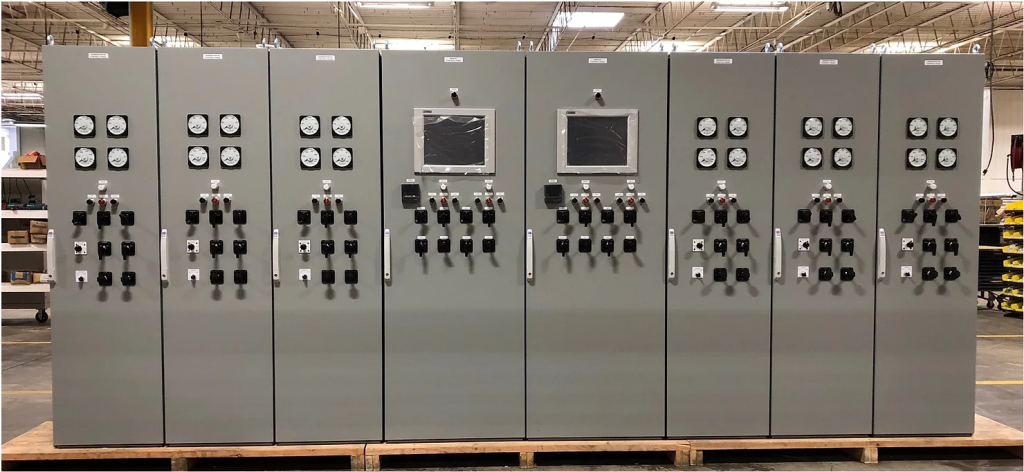
Advances in modern switchgear technology aims to reduce unexpected downtime by providing real time status of the energy condition and resources available to keep the “lights on”.
Innovations in electrical switchgear can increase efficiency, reduce human workloads, improve environmental outcomes, and give operators more data and control. We’ll take a look at some of the most important advances in switchgear technology occurring today and how they benefit their different use cases.
Increased Digitalisation
While initially not a forerunner of the Industrial Internet of Things (IIoT), which focused more on capital-intensive rotating equipment, electrical switchgear has recently become increasingly digitized. This has come about via embedding new technologies in custom- built switchgear and retrofitting older equipment.
The digital components include microprocessor based controllers with built in communication modes, enabling remote data collection to building management software where analytic software tools can further prompt facility managers to make system wide adjustments remotely. The addition of these digital controls gives operators real time information on the status of the power resources while limiting direct physical contact with electrical switchgear. Remote operations can include opening and closing of circuit breakers, remote racking of breakers, load shedding non essential feeder loads when power availability is limited, to initiating a pre-emptive disconnect from the utility power grid during a storm and placing the facility in storm anticipation mode where the sites emergency generators can be brought on-line in the event of the local utility power having an outage due to storm conditions.
Advanced software simulators can create a ‘digital twin’ of a facility’s electrical switchgear. Using historical data, the digital copy of a substation’s electrical distribution system for example, can be put through analytical modeling reviewing long-term usage, issues, and expected component deterioration. This provides a road map for preventative maintenance programs to watch for potential issues based on total operation time and kW routed through the switchgear. The goal to avert costly, unplanned shutdowns due to unexpected failure of a component within the switchgear.
By capturing and analyzing data in real-time, programs can be set to respond automatically to switchgear and process conditions, reducing labor hours, improving efficiency, and driving better decision-making.
Eco-friendly Switchgear
Addition of complex load sharing algorithms in the switchgear paralleling controllers aides in reducing the number of generators on-line to the minimum number to support the total load demand of a facility. Generators can be brought on-line in parallel with a utility power source to limit the amount of power purchased from the utility while supporting the facility load with on site power generation. As the load fluctuates, in real time, the digital controllers can walk-off generators to match the load, reducing the total carbon emissions for the facility while supporting the needed power loads.
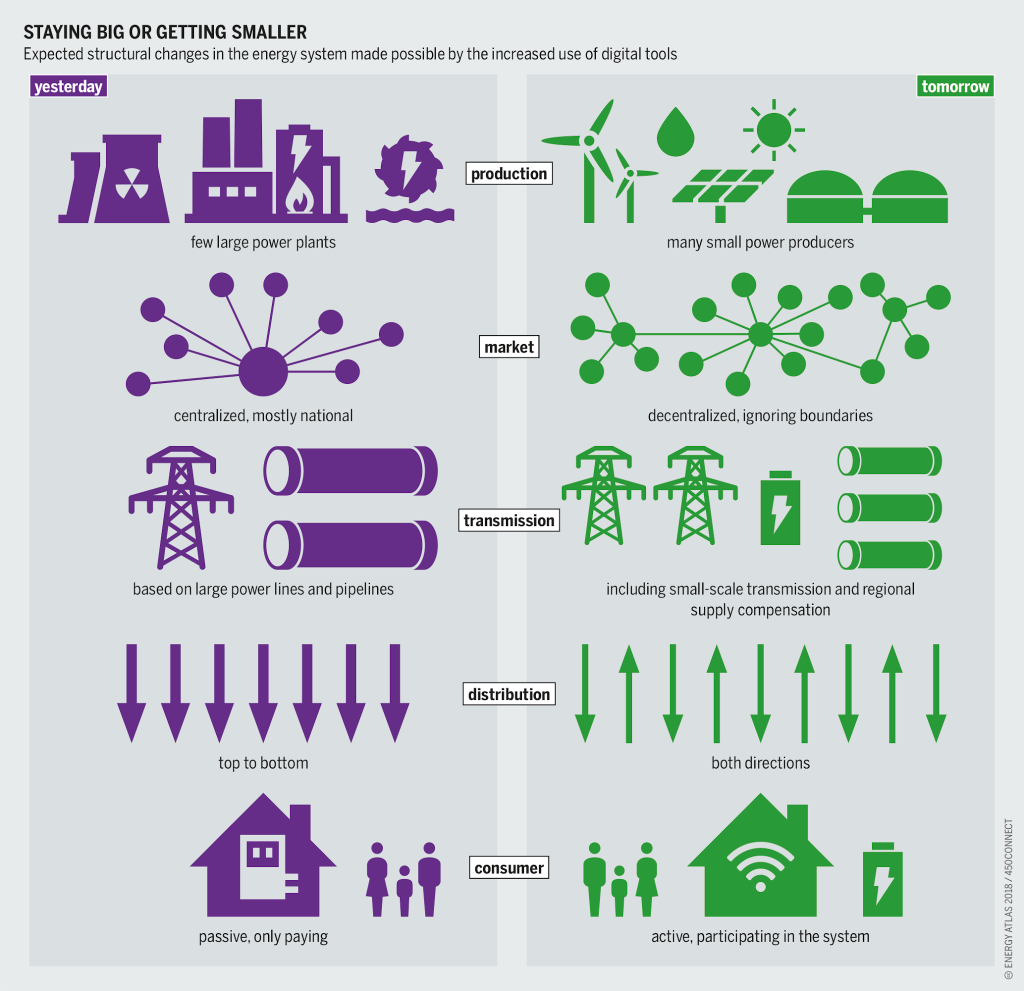
Better Integration
Internet of Things (IoT) links multiple devices together to create a larger network of assets, for power generation, controls and switchgear; this means more visibility in real time for a plant operator to choose which power generation or power resource to utilize to support a facility’s loads. Time of day rates from utility networks, peak demand costs vs fuel consumption and maintenance per hour on standby diesel generators or availability of solar power from photovoltaic panels to even reserve power from on-site battery storage could be managed to provide the best economical usage for time of day and load. All managed remotely or even automatically based on a facility operator’s preferences.
Modular Design
Innovative design and computer aided drafting tools have yielded space savings over traditional switchgear lineups. Compact and modular designs can also provide flexibility to a site to add circuits without a larger footprint or adding building square footage to accommodate more switchgear. 3D modeling allows switchgear designers to review the orientation, space and total materials before spending costly production hours and materials to build switchgear the traditional way, one piece of copper bar stock at a time. Digital designs can be reviewed and analyzed for structural bracing, cost calculations, ampacity and thermal impact until the optimum solution is submitted to production. Saving time and materials on the production floor from costly rework issues. Compact switchgear designs take up less space on the floor of a facility, in the example of a data center where additional free space could be used for more server racks which translates into more revenue for a data center operator.
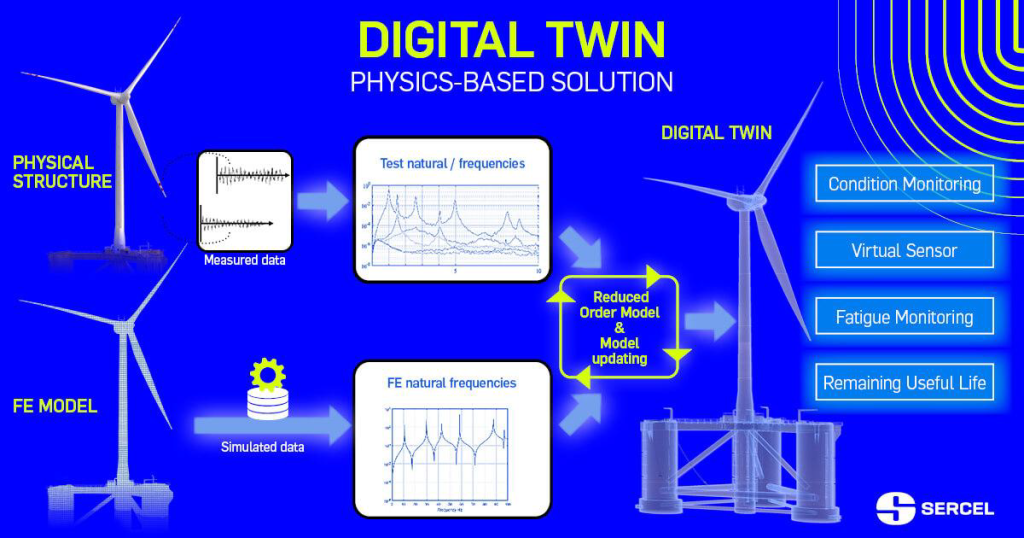
Conclusion
The Industrial Internet of Things is having a considerable impact on how electrical switchgear is made and used. Innovations including embedded controls and connectivity that feed data to remote centers for real time decision making. These advances in electrical switchgear have increased their functionality and delivered greater business value.