Independent Performance Testing
In order to determine the corrosion resistance of various protection methods used on conduit bodies, Emerson turned to Intertek, an independent Total Quality Assurance provider to industries worldwide with more than 1000 laboratories and 44,000 employees. Intertek conducted ASTM-B117 Salt Fog performance testing on iron conduit bodies from three major manufacturers. A total of 39 conduit bodies were tested, all in the 3/4-inch trade size.
The salt solution used was 5% plus/ minus 1% according to ASTM B117-18 “Standard Practice for Operating Salt Spray (Fog) Apparatus.” To prevent salt-fog from entering the interior of the conduit body, all iron test samples had steel (zinc-plated) plugs installed, with aluminum plugs with Teflon® tape in the aluminum samples. Test samples were subjected to the salt-fog for 1008 hours (42 days), being removed only for inspection and photography at fixed intervals.
All testing was conducted in the Arlington Heights, Illinois (USA) Intertek laboratory in January 2019. Test samples
were sorted into 15 groups according to metal and protection types, i.e., malleable iron (plated/painted), die-cast aluminum (painted), cast iron (plated/painted), cast aluminum (unpainted), et cetera. All samples were purchased at electrical distributors straight from their inventory and not sourced direct from the manufacturer. In this paper, we will look at the results of the malleable iron and cast iron samples. Results from the other samples will be published in an upcoming white- paper, although those results further bolster the case for triple coat protection.
Final Word: Triple coat is the best defense against corrosion
Not all industries have the same corrosion problems, but all industries do need to take the possibility of corrosion seriously and choose the right protection for their particular operations and environment. Start by checking the certifications and ratings required for your application. Next, discuss these requirements and concerns with the manufacturer. Becoming informed is the best way to ensure the product you select will provide the corrosion protection and service you expect over its lifetime.
Both in this study and in real-world applications, the triple coat finish has shown to be far more effective than conventional paint finishes, without question. It’s formed when a zinc electro-plate, chromate dip and epoxy powder coating is combined to achieve greater corrosion protection in wet or harsh environments, assuring long, trouble-free service in locations such as petrochemical and chemical plants, refineries, and other process industries.
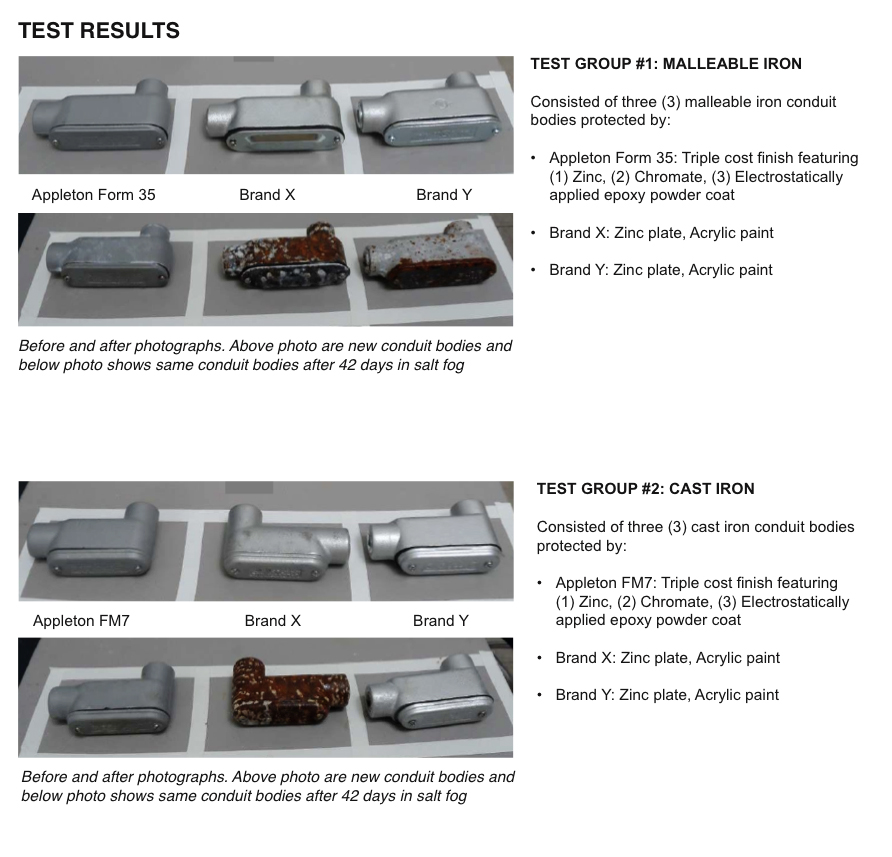
Triple coat finishes consist of:
Coat #1: Zinc Electroplate
Zinc is one of the most important nonferrous metals. When applied onto the surface of ferrous (iron-containing) metals, it creates a formidable corrosion-resistant barrier. It is resistant to atmospheric attack, and fresh and salt waters, and is highly effective at keeping moisture from reaching the surface of the coated object.
Coat #2: Chromate Dip
Chromate coatings act as paint does, protecting the zinc from white corrosion, thus making the part considerably more durable. It also destroys organic growth on the surface. While conventional paint coatings have long been popular, they’re simply not as effective in resisting corrosion as Chromate. Paint is hard to apply evenly, so it tends to drip and bubble, miss small crevices, and thin out at the edges, leaving these areas more exposed. Because of its chemical composition and method of application, Chromate is not subject to paint’s limitations.
Coat #3: Epoxy Powder Coat
As a final finishing step, Epoxy powder is applied to fittings electrostatically. Drawn to the metal like a magnet, the powder covers evenly, reaching into the smallest crevices. The powder is then slowly oven-baked to cure the coating and ensure a strong bond. Because powder coating does not have a liquid carrier, it can produce thicker coatings than conventional liquid coatings without running or sagging. Products are more resistant to mechanical damage since the powder coat finish does not crack or chip like painted surfaces.
By merging the strengths of Zinc, Chromate and Epoxy Powder, the triple coat process results in a thick, uniform layer of protection that seals out the harshest corrosives, including:
- Sulfur oxides
- Nitrogen oxides
- Chlorine and chlorides
- Ammonia and ammonia salts
- Hydrogen sulfide.
Triple coat is extremely durable. It is flexible so it stays intact when the underlying metal expands and contracts during temperature changes and stress fluctuations — unlike paints. It also adds value through fewer callbacks and lower operation costs, while helping to safeguard the environment by virtually eliminating overspray particulates. On the job, there is no better way to safeguard your operations, profitability and employee safety than triple coat protection.