IN THIS ARTICLE WE EXPLORE THE CURRENT USE OF HYDROGEN in industrial processes, as well as its role in the ongoing global transition to a net zero economy. We’ll provide insights into market opportunities and challenges, the latest processing technologies, and best practices in safety to help industry stakeholders as they face mounting pressure to scale up hydrogen production.
Hydrogen can be very dangerous. At every point across its value chain, upstream and downstream, hydrogen remains extremely combustible and can explode in confined spaces when exposed to any electrical equipment producing arcs, sparks or excessive heat. Consequently, correctly certified explosion-proof electrical equipment is required as defined in the NFPA 70 National Electrical Code (NEC Article 500), among others depending on geography. For the purposes of this article, we will concentrate on NEC requirements for hydrogen, specifically Class I, Division 1 or 2, Group B.
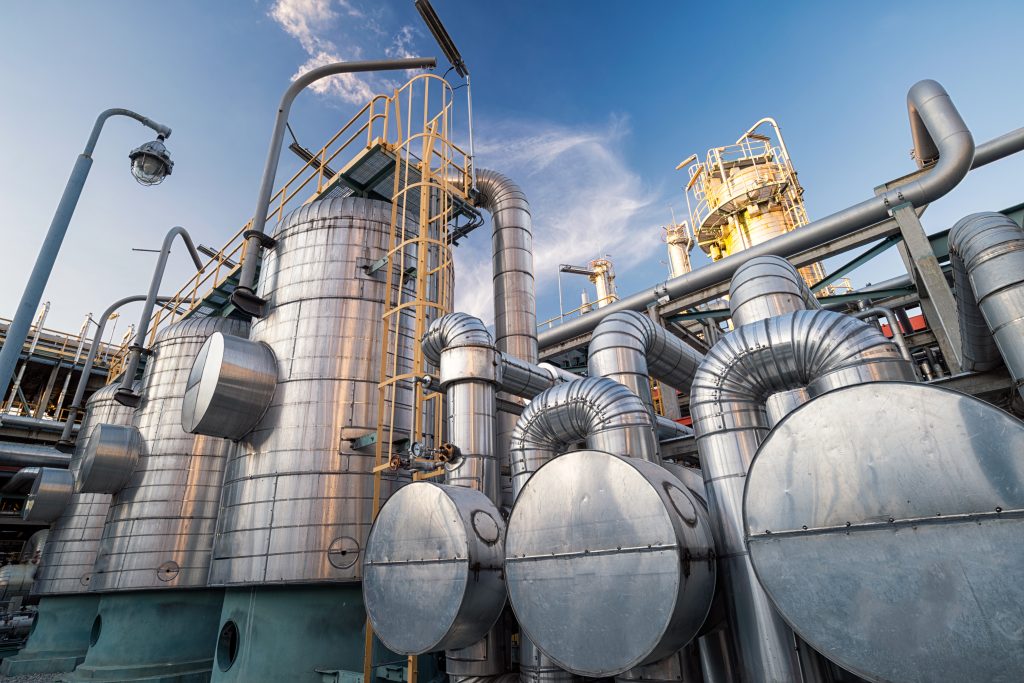
The Hydrogen Market
According to the International Energy Agency, hydrogen represents “the biggest innovation opportunity” to reduce or eliminate carbon dioxide (CO2) emissions produced by human activity. Hydrogen’s ability to replace fossil fuels without releasing CO2 when consumed has led to new applications being explored on numerous fronts, notably fuel cell electric vehicles. Bolstering these initiatives, the U.S. Department of Energy in 2023 announced an investment of $7 billion to launch seven Regional Clean Hydrogen Hubs to accelerate the commercial-scale deployment of low-cost, clean hydrogen.
While green innovations like these hold great promise, hydrogen as an alternative energy represents only a small sliver of overall consumption. Of the 120 million metric tons (MMT) of hydrogen consumed worldwide in 2022, the vast majority was concentrated in the traditional sectors of petroleum refining and chemical processing. Globally, each year approximately 55% of hydrogen goes into the creation of ammonia for fertilizer, another 25% into petroleum refining hydro-desulfurization and hydrocracking operations, 10% to produce methanol, and the remaining 10% in treating metals, flat glass manufacturing, chemical synthesis of plastics, and the manufacturing of semiconductors. Gaseous hydrogen is also utilized as a coolant for generators due to its high thermal conductivity.
Almost all the hydrogen produced in the United States is used for refining petroleum, treating metals, producing fertilizer, and processing foods.
Hydrogen Production
Hydrogen is the simplest and lightest of all Earth elements, consisting of only one proton and one electron. It is also the most abundant element in the universe, yet rarely in its pure state. Instead, hydrogen covalently bonds to one of three elements: fluorine, oxygen, or nitrogen. To produce hydrogen as fuel, it must be separated from the other elements in the molecules where it occurs. Technologies enable the separating of hydrogen gas from its companion substances in purities in the order of 99.999%.
Hydrogen is almost exclusively produced through thermochemical processes requiring fossil fuels: hydrocarbon reforming, coal gasification, hydrocarbon pyrolysis, and plasma reforming. Approximately 95 percent of hydrogen is produced via steam reforming of hydrocarbons with the balance coming from water electrolysis, biomass-derived liquid reforming, and microbial biomass conversion.
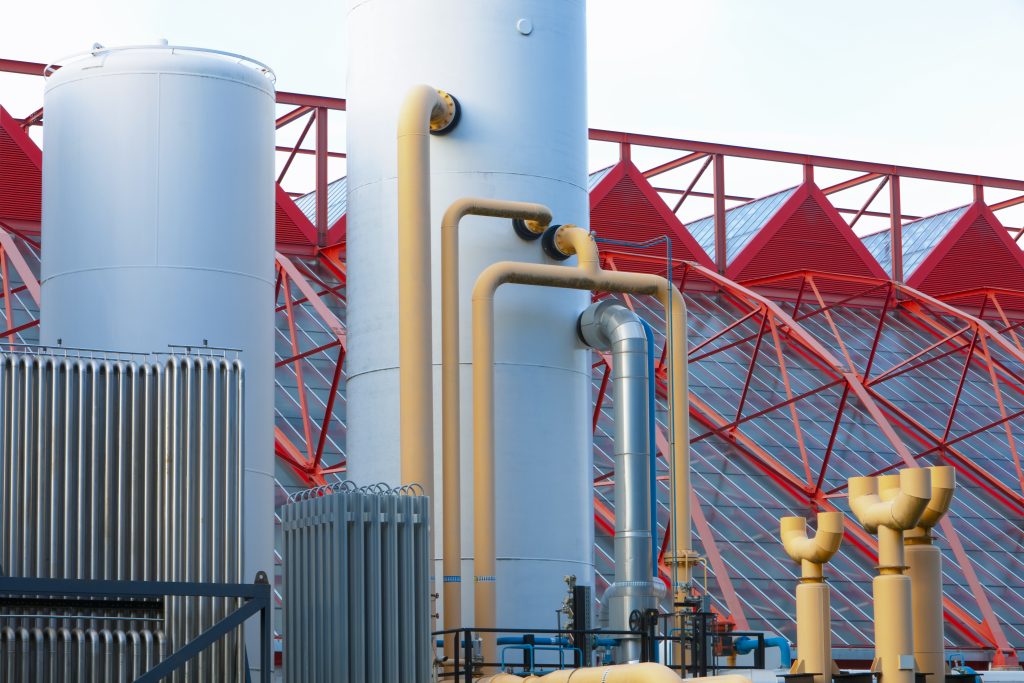
The least expensive method of production is steam methane reforming (SMR). Besides methane, it is used to produce hydrogen from ethanol, propane and gasoline. Although steam refining is very cost-effective, it requires fossil fuels as feedstock and to produce heat. In fact, for every kilogram of hydrogen produced in SMR, seven kilograms of CO2 are released into the environment. Capture and Storage techniques (CCS) seek to trap the vast majority of CO2 produced by SMR and store it in the ground, converting the product from “gray” to “blue” hydrogen.
An alternative to steam refining is water electrolysis. This pathway splits hydrogen from water using electrical current, effectively converting electrical energy into chemical energy. Depending on the kind of electrolyte material and ionic species being used, electrolysis is carried out using one of three types of electrolyzers: alkaline, solid oxide, or proton exchange membrane (PEM). Like steam refining, electrolysis largely relies on fossil fuels. The only way the process is CO2 neutral—that is, it produces almost no greenhouse gases or other pollutants—is when renewable energy sources are employed, such as wind or solar. Because this “green” hydrogen approach is considerably more expensive than hydrogen sourced from fossil fuels, it makes up less than 0.04% of all hydrogen produced globally.
Hydrogen Production Color Codes
Different methods of producing hydrogen are often referred to by certain colors:
- Brown hydrogen — Produced from the gasification of coal. Releases large quantities of CO2.
- Gray hydrogen – Produced by mixing fossil gas (natural gas, methane) with steam. Releases large quantities of CO2.
- Blue hydrogen – Produced using the same method as gray hydrogen, but with carbon emissions captured and 12 | Electrical Products & Solutions | MAY 2025 stored (CSS) underground.
- Green hydrogen – Produced by passing electricity generated from renewable sources through water, resulting in very low or no carbon emissions.
- Pink hydrogen — Like green hydrogen, this process incorporates electrolysis, but uses nuclear rather than renewable energy sources. Hydrogen can be used as a feedstock and energy source with no greenhouse gas emissions.
Hydrogen Storage
Hydrogen may be physically stored as a gas or a liquid, yet both methods present challenges. Low energy density and the complexities of cryogenics are some of the biggest barriers. Hydrogen gas is prone to leakage. It can permeate through solid metals, as well as embrittle metals, which affects the integrity of storage and transportation infrastructure by creating cracks. Even a tiny leak can lead to the accumulation of dangerous hydrogen clouds in a confined area or within an enclosure.
Another storage option is to chemically bind hydrogen with solids or liquids able to absorb it.
Finally, there is the underground storage of hydrogen. Bulk storage of uncompressed hydrogen has proven viable in salt caverns, and to a lesser extent in porous media such as sandstone or shale, and in engineered cavities.
Hydrogen Transportation
Most hydrogen used in the United States is produced at or close to where it is consumed—typically at petrochemical or chemical sites. If it isn’t consumed at its point-of-production, hydrogen can be transported to its point-of-use by railcar, barge, or over the road in gaseous tube trailers or in cryogenic liquid tanker trucks. Long-distance pipeline investments have been made in areas where there is a significant, steady demand for hydrogen. In the United States, there are approximately 1600 miles of active pipeline for hydrogen transportation, 90 percent of which is located along the Gulf coast of Texas, Louisiana and Alabama, serving refiners and ammonia plants. Pipelines are the least expensive method of transporting hydrogen.