ACCORDING TO U.S. BUREAU OF LABOR STATISTICS, the demand for electricians is expected to grow by 7% from 2021 to 2030.1 At the same time, however, labor shortages continue to be a challenge for the electrical industry. The COVID-19 pandemic greatly agitated this issue, with many experienced electricians deciding not to return to the workplace after initial shutdowns, instead choosing early retirement.
Additionally, new electricians are not currently entering the industry at a rate high enough to offset this increased influx of retirees. According to industry experts, the prerequisite hands-on experience needed to become a Journeyman Electrician, combined with a perceived lack of workplace flexibility, is deterring younger generations from entering the field.2 Trade school interest is also on the decline, as many young people are instead opting to pursue a degree from a college or university.
On top of accelerated premature retirements, post-pandemic supply chain issues continue as material shortages delay shipments of individual parts. Contractors that would normally request their parts from one facility are being forced to order from multiple vendors, increasing the likelihood of supply chain mishaps. More than 50% of an electrician’s day can be lost due to supply chain issues.3 As a result, many more electrical contractors are turning to prefabricated solutions to help mitigate these labor shortage and supply chain problems.
Here are five reasons why electrical contractors should consider using prefab materials for their next project:
1. Prefab Saves You Time
Prefab saves time by reducing the amount of labor hours required for a typical job, specifically through installation. In a traditional assembly environment, contractors have to gather individual components for a job, organize them, and transport them to their jobsite. With prefab materials, the components are delivered to each site pre-wired, only requiring mere branch connection. Since prefab solutions are manufactured offsite in a controlled environment, this allows for increased onsite productivity and improved management of asset-based labor.
Transportation of materials is also a more organized process, as the consolidated components can be delivered at once rather than at separate times, leading to a more streamlined schedule and productive delivery process. With prefab solutions arriving at job sites already constructed, electricians can focus on broader tasks while conserving brain power, time, and energy.
2. Prefab Saves You Money
Prefab materials are not only more efficient for manual labor, but also more efficient for project budgets. With employees working faster, projects become less susceptible to inconvenient events such as weather delays or site delays due to pending permits. The concrete cost is more predictable as well. According to Dodge Data & Analytics’ 2020 SmartMarket Report, 81% of firms and contractors agree that prefabrication provides significantly improved cost predictability.4 Without unrelated disturbances or setbacks, contractors will be more likely to predict exactly what a job will cost to complete, resulting in a more organized, standardized process. When it comes to prefab solutions, saved time equals saved money.
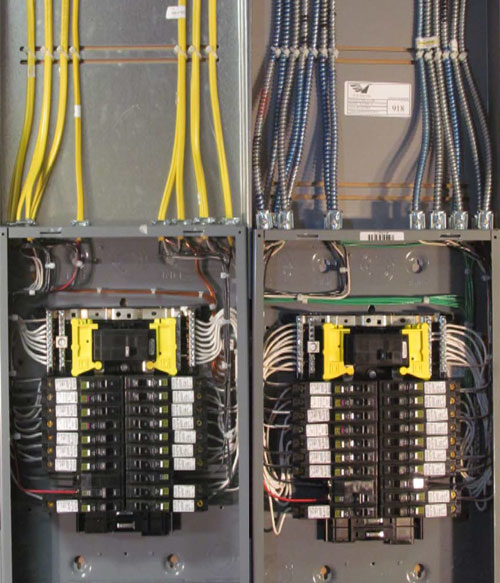
3. Prefab Improves Jobsite Safety
Prefab solutions mitigate various safety risks for all involved on the project, as the reduction of job installation time and required manual labor hours leads to a decreased potential for safety hazards. The less time workers spend wiring and manufacturing, the less likely they will be to injure themselves. The prefab process itself dramatically minimizes the possibility of onsite hazards.
Prefab materials also help to eliminate potentially dangerous remnants of wiring that would otherwise be left behind. Since prefab projects are primarily completed on the ground level, workers also will not need to climb ladders as often, decreasing the likelihood of one falling on the job. Additionally, reducing the man hours required for a project will lessen the chances of employees becoming overworked and fatigued, which could otherwise lead to a jobsite injury. Overall, prefab solutions make for a cleaner, safer worksite.
4. Prefab Increases Your Competitive Advantage
With improved efficiency metrics across the board, prefab means that contractors can plan and manage projects more effectively—a large factor in establishing new business. Shaving down project timelines and properly aligning with strict schedules can result in a competitive edge. Dodge Data & Analytics’ 2020 SmartMarket Report reported that 80% of firms and contractors agreed that prefabrication increased client satisfaction.
Since prefab materials result in a much more efficient use of time, the general quality of each project increases. Customers want the best results as quickly and as cost-effectively as possible, and prefab materials are able to help meet these standards. Modifications, add-ons, and changes are executed easier with prefab than they would be with manual wiring. The modular format of prefab wiring is assembled in a way that allows for simplified rewiring and quick reinstallation.
5. Prefab Allows More Efficient Project Planning
The coupling of Building Information Modeling (BIM) technology with prefab materials compounds worksite productivity by digitizing the entire lifecycle of a project. BIM Service Providers are essential in the planning and execution of projects that utilize prefab materials due to improved precision and elevated design abilities. Contractors can preassemble a project’s entire electrical distribution framework from comprehensive 3D renderings that provide exact measurements of the materials.
The ability to visualize which elements of a project are suitable for prefab materials is crucial in the first stages of planning. 3D digital images of jobsites can easily detect early-stage errors and promote collaboration with the added benefit of shareability for the entire work team. BIM technology enables electrical contractors to identify the specific products they need for their designs by selecting the correct attributes every time. This virtual tool then calculates the hardware needed and outputs the exact part number. BIM tools greatly expedite jobsite installation and pre- project planning.
By drastically improving jobsite efficiency, prefabricated solutions allow electrical contractors to work smarter not harder. As contractors continue to deal with labor shortages and supply chain issues, prefab, especially when combined with digitized tools like BIM technology, delivers numerous advantages for all team members involved on a project, both on and offsite.