EMERSON’S SOLUTION Nelson™ Heat Trace Type LT Self-Regulating Heater Cables by Emerson are the field-proven solution to safely maintain fluid flow over a wide range of operating temperatures. They have been relied upon for more than 20 years by the hydrocarbon and chemical industries.
Suitable for use on pipes, tanks, and vessels, Type LT cable maintains process temperatures up to 121 °C (250 °F) to meet viscosity/fluid requirements. In addition, the cables provide freeze protection of periodically steam-cleaned components, as well as for structural anti-icing. The cables provide a conductive ground path when installed on non-conductive surfaces, such as plastic or painted pipe.
Type LT cables are self-regulating, meaning that they will adjust heat output automatically in response to surrounding temperatures. The heater cable derives its self-regulating characteristic from the inherent properties of the conductive core material. As the core material temperature increases, the number of conductive paths in the core material decreases, automatically decreasing the heat output. As the temperature decreases, the number of conductive paths increases, causing the heat output to increase. This occurs at every point along the length of the cable, adjusting the power output to the varying conditions along the pipe. Straight line runs are the common majority for installation types, however the older practice of spiraled around the pipe installation is also acceptable. Because the cable is self-regulating, it can be overlapped where the installation requires, without creating hot spots or burn out.
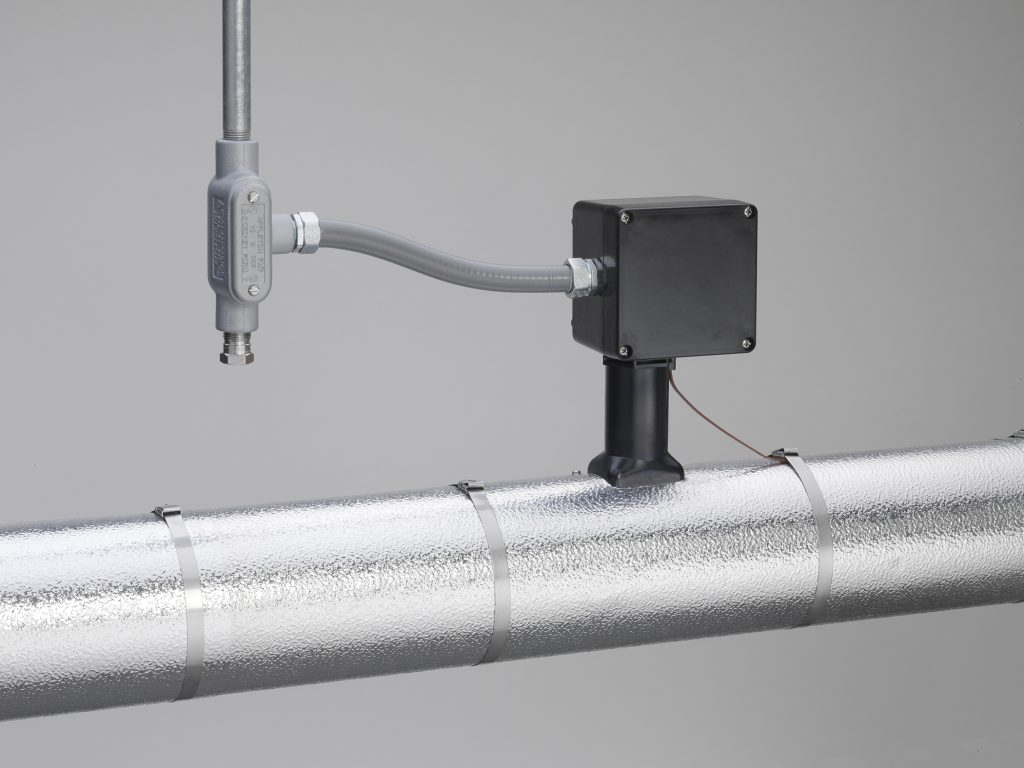
Heat Trace Cable Installation
Before installation, consult with the manufacturer’s specific instructions. Failure to do so will likely void warranties and agency approvals. The integrity of the system depends upon how accurately the heat trace cable is installed. Improperly installed systems have resulted in system failure and physical injury.
In general, heat trace cables can be installed in either straight runs (found to be the more standard industry protocol) or spiraled around the pipe. Spiraling is used when a limited number of cable types are available and has become less common in recent years. In straight tracing, the cable is installed on the lower quadrant of the pipe to prevent physical damage from falling objects or from being walked on. In both spiraling and straight runs, the cable should be applied flat to the pipe.
Attachment of the cable to the pipe can be done with fiberglass tape or plastic wire ties provided the plastic has a maximum temperature rating equal to or better than the system requirements. The cable should fit snuggly against the pipe and be secured every 12 inches. It is recommended that metal straps, wire, vinyl electrical tape, or duct tape not be used to attach the cable to pipes. If the cable must be cut, do so after it is attached to the pipe, and after confirming allowances for terminations, connections, and heat sinks. Loop the cable around valves, hangers, and other small in-line devices in a manner that allows their removal or access without having to cut the cable.
Moisture penetration of the heat trace system is the single largest source of problems in wastewater treatment facilities. Particular care must be given to the proper sealing of all electrical connections and splices. Cable sealing kits will provide a proper seal for the cable itself, while other electrical connections, including heater to power wiring, thermostat connections, and panel and breaker connections, should be sealed or moisture proofed in an approved fashion.
After installation, it is important you inspect the cable and system components for any possible damage, ensuring the cables are free of nicks, tears, or gouges. Verify that additional cable has been installed at each valve, flange, pipe support, and other devices to allow easy access to the device making sure connections, splices, and end-seals meet code requirements.
The above are only general recommendations. Again, it is very important to consult with the heat trace cable manufacturer’s user manual for specific installation instructions.
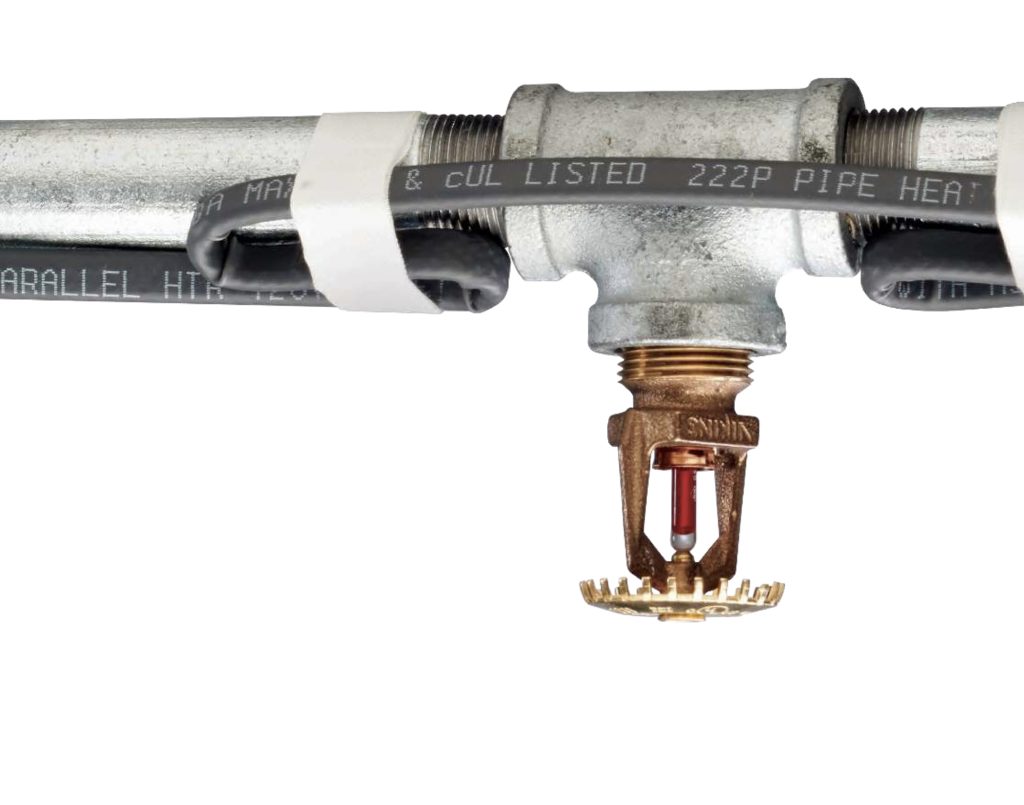
Thermostats and Controllers
WWTP heat tracing requires the use of temperature control. When selecting the proper thermostat or controller you must consider the voltage and amperage ratings of the device as well as the suitability of its housing for the environment, specifically, if the enclosure is explosion-proof, raintight, and corrosion-resistant.
Emerson’s Solution
The Nelson Heat Trace CM-1 Microprocessor Based Heater Cable Monitoring System by Emerson continually monitors the supply voltage and current of both series and parallel styles of electric heat trace cables and panels. When used in conjunction with ground fault branch breakers, the CM-1 also serves as an automatic alarm system when the heating system is de-energized due to a tripped breaker. Continuity monitoring for parallel-resistance heating cables can be enabled by adding a passive bus monitor device at the end of each heater circuit. The microprocessor-based scanner systematically compares programmed values with actual data from sensor cards capable of monitoring up to 4 circuits each. The status of each circuit is displayed using high-visibility LEDs. Multiple CM-1 systems throughout a facility can also be connected to a central PC to provide centralized alarm status and acknowledgment. It features a NEMA 4 or 4X powder-coated or stainless-steel enclosure for wet environments.
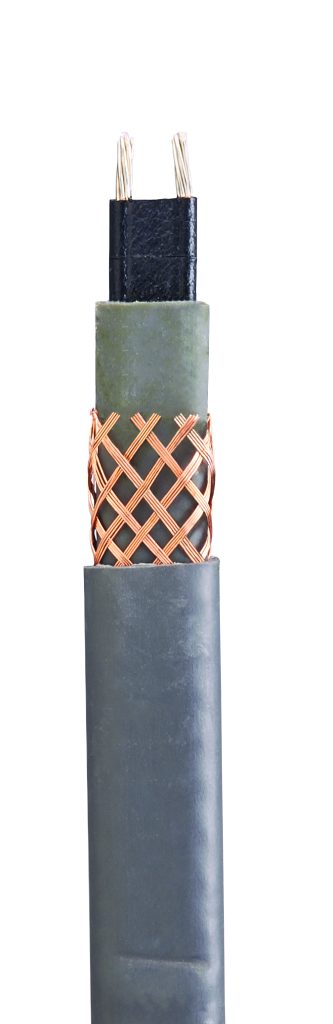
Temperature Maintenance
Although the application we are addressing in this white paper is freeze protection, it should be noted that many chemicals (aluminum, ferric chloride, sulfates, and polymers) used in sewage treatment are highly aggressive and require process temperature maintenance, a task where electric heating trace cables also excel.
Conclusion
Wastewater treatment is one of the most important environmental conservation processes available today to address the growing crisis of water scarcity. WWTP ensure that the sewage discharged from homes, businesses, and industries is properly treated before it is released back into local waterways. During colder months, heat trace cables help maintain efficient system performance and counter-seasonal upsets by keeping water and chemicals flowing, therefore preventing facility flooding, the expense of replacement parts and repairs, environmental damage, and plant downtime.