A DECREASE IN MACHINE AVAILABILITY due to power quality issues disturbs the natural flow of manufacturing, leading to lost productivity, increased maintenance requirements and eroded customer trust.
Machine downtime is the single largest source of lost production, typically accounting for almost 5 percent of factory losses—although many manufacturers lose more. For example, when the cost of equipment replacement and parts, labor, maintenance, delays, sales and production are added up, downtime can exceed $10,000 per hour.
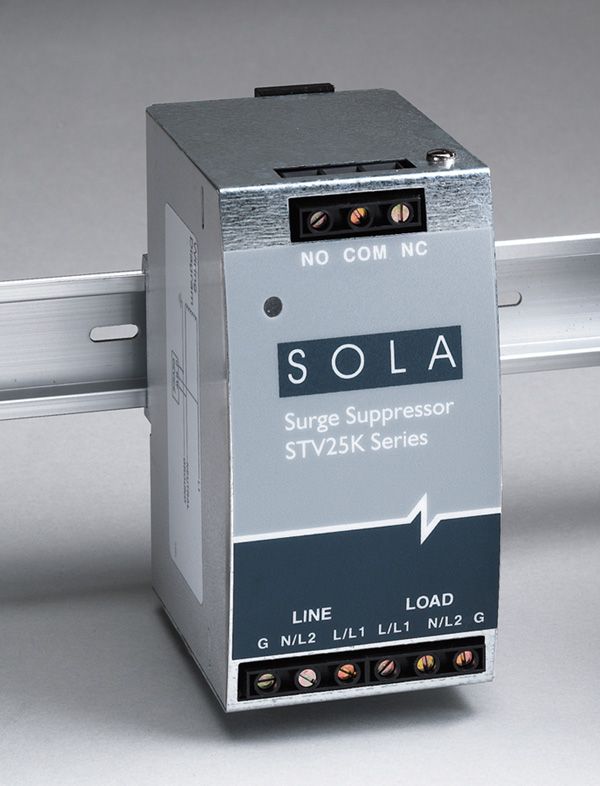
With such high costs at stake, keeping machinery operating smoothly is critical to the bottom line. OEMs who focus on improving their machine availability through monitoring overall equipment effectiveness (OEE), as well as deploying power quality strategies, will strengthen their competitive position and customer relationships.
Elements of OEE
Power quality falls under the category of OEE, which is a best practices metric that identifies the percentage of planned production time that is truly productive. An OEE score of 100 percent represents perfect production: manufacturing only good parts, as fast as possible, with no downtime. OEE is a simple yet powerful roadmap that helps production floor people and management to visualize and eliminate equipment losses and waste.
Calculating OEE begins with establishing Planned Production Time (PPT). PPT is total time minus the time when the manufacturer has no intention of running production, such as lunches, employee breaks, scheduled plant shutdowns or when there are no orders to produce. To establish the OEE of a machine or process, its PPT is scrutinized targeting the lean manufacturing goals of reducing productivity losses by factoring in availability, performance and quality using this formula: OEE (%) = availability ratio x performance ratio x quality ratio.
Availability Ratio
Availability has to do with any event that halts scheduled PPT for several minutes or more, whether the events are “planned” i.e., die changeovers, or “unplanned” such as machinery failures or a shortage or materials.
As an example:
- PPT is 10 hours (600 minutes)
- Downtime = Machine breakdown is 30 minutes, changeovers are 30 minutes, stoppage is 30 minutes. Total of 90 minutes
- Available time is 600 – 90 = 510 minutes
- Availability ratio: 510 minutes divided by 600 minutes or 85%
Performance Ratio
Performance takes into account any thing that slows down the manufacturing process like jams, breakdowns, accidents or basic machine wear. This total is subtracted from standard output. Standard output is the best output rate known to be produced on the machine, regardless of whether that is above or below design speed.
For example:
- Standard output is 3 parts per minute x available time (510 minutes) = 1530 parts
- Actual output (defects and good parts) = 1250 parts
- Performance ratio is 1250 parts divided by 1530 or 81%
Quality Ratio
Finally, there’s quality. This ratio measures defective parts like scrap, rejects, or parts that need reworking, to good parts.
Example:
- Actual parts output is 1250
- Defective parts are 150
- Quality ratio is (1250 – 150) divided by 1250 or 88%
Therefore, OEE of the machine is 85% (availability) x 81% (performance) x 88% (quality) = 55.4%.
While many manufacturers have risen to the challenge of improving OEE by honing in on basic availability, quality and performance issues, one area that has remained largely elusive is the role power quality plays in all three. After all, how do you judge the quality of such an unseen commodity as electricity?
Understanding Total Power Quality
Power quality ensures that the needs of a facility are met by the existing source of electricity from the service entrance to the most critical production equipment. Power disturbances such as voltage transients, surges and spikes, harmonics and voltage imbalance will have an impact on the quality of electricity, and therefore, carry the potential to disrupt production, damage manufacturing equipment and corrupt data in automated environments. By conditioning incoming power, however, plant operators can be assured against outages and disturbances that can interrupt machinery availability and cause shutdowns mid-process.
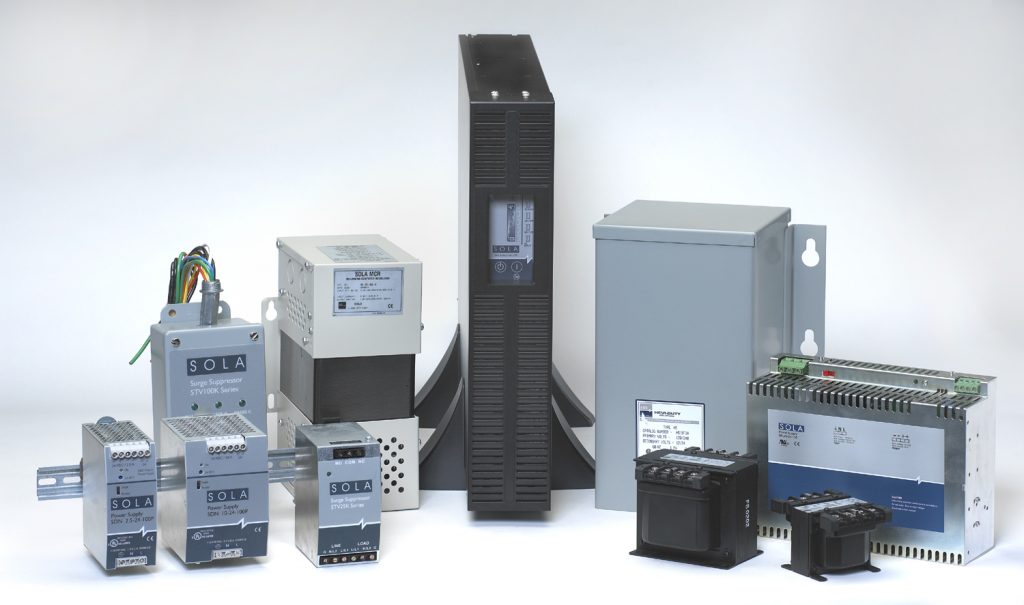
The only way to mitigate the risk of poor power quality is to have the right technology, both for power protection and power conversion, since the power conversion choices made upstream can impact the type of power protection required downstream. Power protection plus power conversion results in a solution known as Total Power Quality (TPQ).
A power protection strategy consists of surge protection and filtering devices that protect critical operations across facilities from the continuous threat of transient spikes, noise and harmonic distortion. Employing an entire facility protection strategy safeguards the electrical system against most transients. Multi-stage protection involves clamping the initial high energy surge, filtering any remaining noise or transients to the protected sensitive equipment, and finally, protecting the data/signal lines entering or leaving the control panel or the factory floor. This coordination of devices provides the lowest possible let-through voltage to the equipment ensuring maximum productivity.
Surge Protection: These devices focus on limiting high-voltage spikes to a level that is acceptable to most electronic equipment. Plus, they’re a great first line of defense, using components that are placed in parallel with the line and serve as clamping mechanisms for high-energy impulses. Surge protective devices are typically installed at service entrances, on larger distribution panels and at the point of use as recommended by Institute of Electrical and Electronic Engineers (IEEE) in their Emerald Book (Standard 1100-2005): Recommended Practice for Powering and Grounding Electronic Equipment.
Filters: Low-energy transients and high-frequency noise (also referred to in the industry as electronic rust) are the primary causes for system disruption and long-term degradation of microprocessor-based equipment within a facility’s processes, for instance, PLCs and motion control systems that require clean AC power. Protection calls for the use of active tracking filters that attenuate impulses that would normally go untouched by standard, parallel clamping devices to limit stress and the electronic rust that degrade electronics.
Data/Signal Surge Protection: Networked industrial operations require error-free transmission of information for maximum productivity and integrity of data, but these areas are often overlooked when it comes to power protection. The importance of protection at this level grows with the manufacturer’s reliance on sensitive instrumentation, networked automation and uncorrupted data transmission increases with the adoption of Industrial Internet of Things (IIoT) systems. Data/signal line surge protection devices are used as the final part of the multi-stage protection strategy recommended by IEEE practices which involves clamping the initial high-energy impulse, filtering any remaining noise or transients to the PLC or sensitive equipment and finally, protecting the data/signal lines entering and leaving the control panel.