IN ANY MINING OPERATION, the facility’s infrastructure relies heavily on electric power. However, mining’s harsh conditions, non-linear loads, extensive use of long cables for mobile equipment, complex grounding, and the adoption of ever larger machinery with higher power requirements all challenge the reliability of the power mines depend on to keep operations running 24/7, 365 days a year.
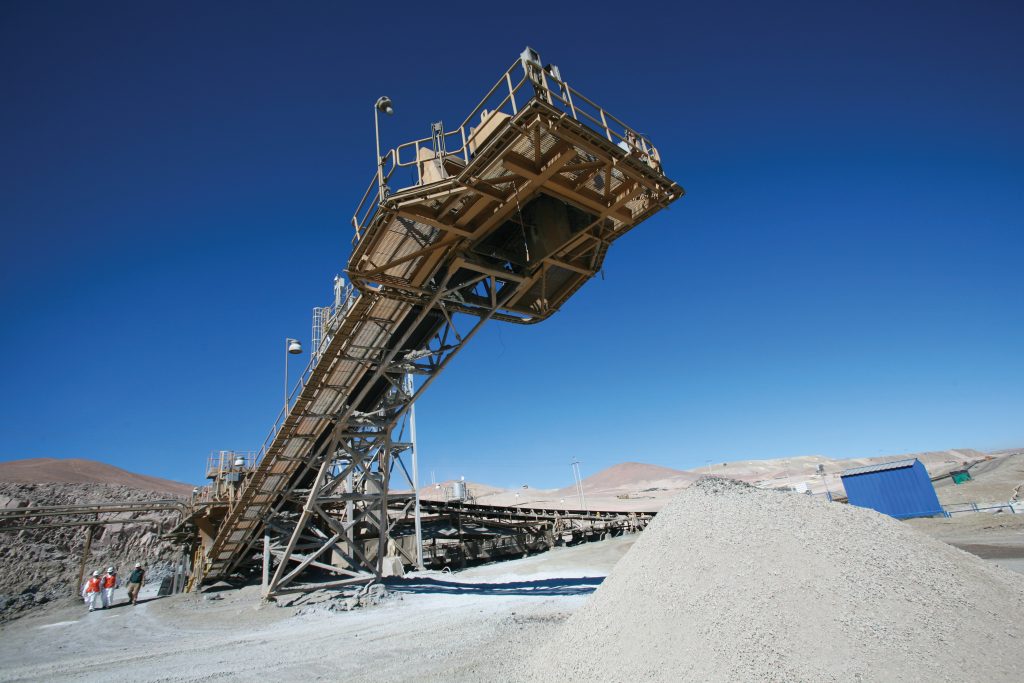
This article will address power reliability in mines and specifically, the increased total cost of operations related to power quality issues. We will explain the four types of power quality disturbances mines commonly experience. Identifying power quality problems is the first step towards developing mitigation tactics that can improve a mine’s safety, reliability, productivity, and cost efficiency.
Power quality is critical in mining, since even short interruptions can lead to equipment damage and production losses costing hundreds of thousands of dollars per hour. Besides downtime, poor power quality can pose safety hazards to workers, especially those underground or in confined spaces. Without reliable power, ventilation and lighting systems may fail or malfunction, making it difficult for workers to see or breathe while levels of combustible gases and dusts increase.
Mining Power Systems
Mines consume tremendous amounts of power, as much as 120 megawatts per 100,000 tons of mined product each day. (4) To get a better idea of power demand, consider the variety of electrical equipment and the different types of loads in mines. In underground mines, the power system must supply locomotives, drills, shearers, crushers, loading machines, belt and shuttle conveyors, roof bolting machines, hoists, chillers, ventilation systems, and pumps. In surface mining, there are power-hungry rope shovels, drills, and excavators. Extracted materials transported to processing plants encounter large crushers, grinding rolls, semi-autogenous grinding (SAG) and ball mills, and exhaust and dryer combustion fans. Understanding the diverse nature and complexity of mining equipment sheds light on why power quality problems are so common.
Mines generate electric power from a variety of sources, sometimes resulting in a patchwork system. When AC grid access first became available, operators began purchasing much of their electrical power from utility plants. High voltage DC power remains in use, mainly for electric rope shovels, uninterruptible power supplies (UPS), and emergency systems, supplied by AC-to-DC conversion or by onsite DC microgrids. Fuel-driven generator sets (gensets) are also commonly used, as are gas fired boilers and renewable energy sources.
When it comes to sourcing power, utilities offer mine operators two major advantages over gensets. First, they do not require the storage and transportation of flammable fuels over many miles of harsh road and terrain. Second, utilities can respond more effectively to load variations beyond the capacity of local generation options which have less capacity and are prone to significant fluctuations in voltage and frequency. Incidences of voltage variation and power outages are more frequent in the mining industry than in most other industries, largely because mines are typically located in remote areas far away from population centers and existing electrical grids. Transmitting electricity over long distances to a mine can result in power loss, voltage drop, interference, and weather-related outages from high winds, lightning strikes, or ice storms. Utility supply switching (breakers, contactors, or taps) can also give rise to damaging voltage surges.
Power systems in mining operations vary greatly but in general, they will follow a basic design: high voltage power coming off the electric grid feeds high voltage transformers that supply a main substation. In turn, the main substation distributes energy to multiple secondary substations as well as directly to the mine’s largest motor loads. Secondary substations supply power to medium voltage loads and to medium voltage/low voltage transformers that connect to motor control centers. At any stage in this distribution there are power quality threats that can enter the system.
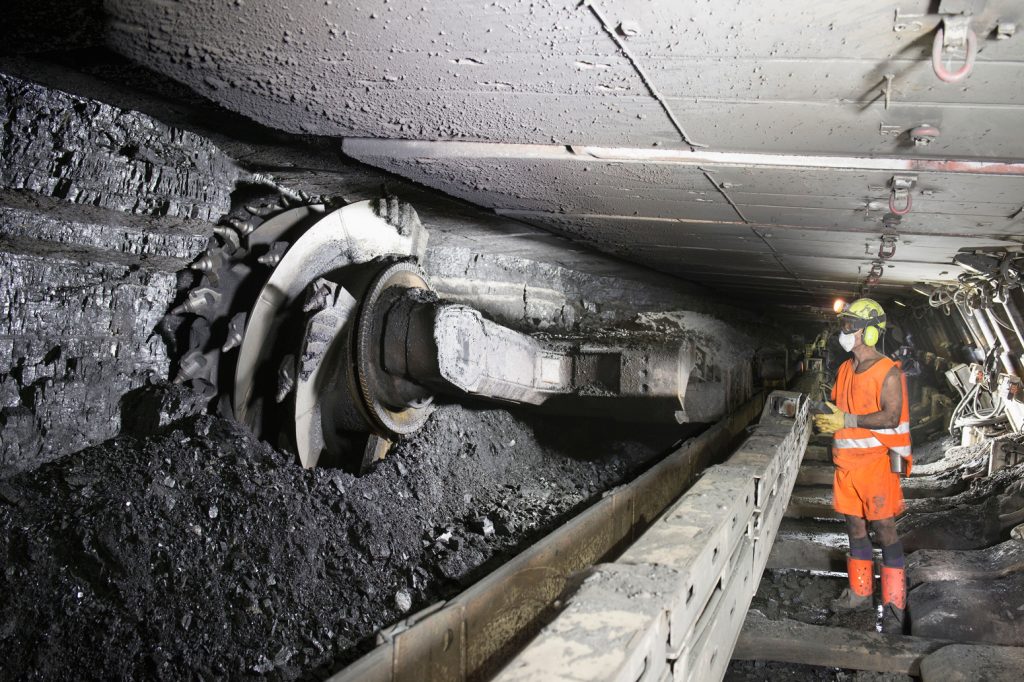
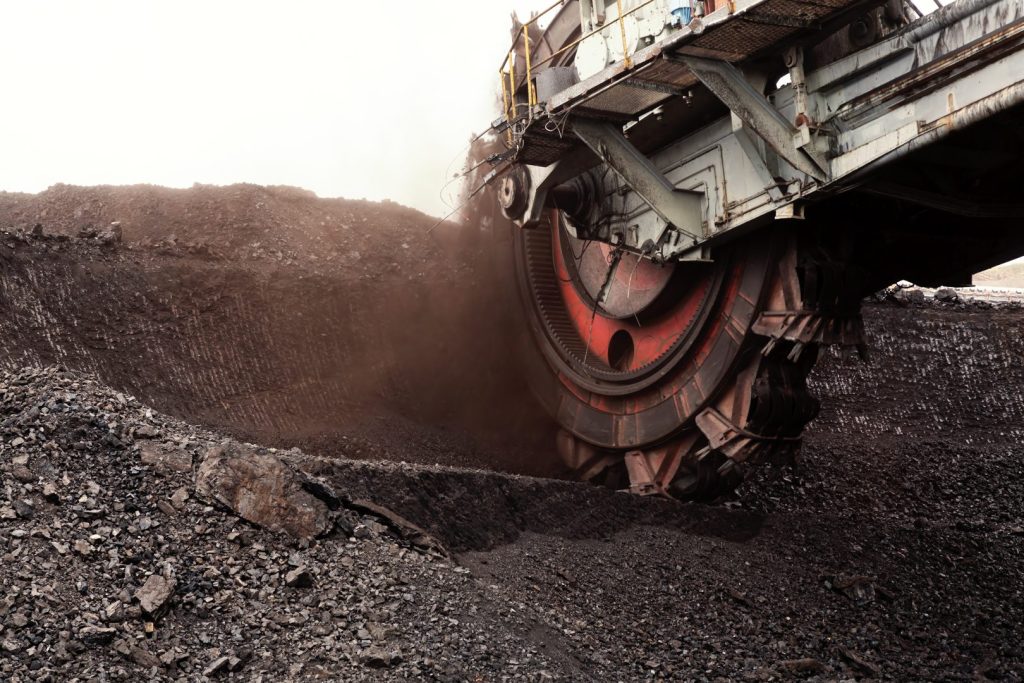
Internal Power Disturbances
While the first inclination of some mine operators is to blame the utility for power quality issues, that view is frequently inaccurate. It’s more common that power quality problems arise from dynamic conditions within the mining facility, manifesting in the form of overvoltage swells, undervoltage sags, harmonic distortion, or total power interruption.
All mine power systems face the challenges of poor power quality. The costly consequences range across operational interruptions, lost data, damaged equipment, and energy inefficiency, to utility fines, reduced productivity, and even worker safety. Due to a mine power system’s complexity, a single power quality solution is rarely adequate to ensure reliable power. The variability of power disturbances therefore requires a multi-tiered approach that often starts by identifying power-offending devices, such as drives, motors, and pumps.
The digital age has come to mining and it brought with it new power quality challenges. Over the past twenty years, the mining industry has implemented more and more automation control within processes. Most of the sophisticated electronics being installed are highly sensitive to power quality disturbances, much more so than traditional machinery. Digital equipment requires protection using tracking filters, surge protective and power conversion products, including K-Factor and Drive Isolation Transformers. Last, but not least, all control panel points should employ surge protection devices.
Common Power Quality Disturbances in Mines
1. Voltage Sags and Undervoltage
Voltage sags and extended undervoltage conditions are the most common power quality disturbances
in underground longwall mining. They occur when a large increase in load current stresses the electrical supply system, causing the supply voltage to drop below levels at which equipment is designed to operate. Voltage sag, as defined by IEEE, is a reduction in voltage for a short time. The voltage reduction magnitude is between 10% and 90% of the normal root mean square (RMS) voltage at 60 Hz. The duration of a voltage sag event, by definition, is less than 1 min and more than 8 msec, or a half cycle of 60-Hz electrical power. (2) Undervoltage events are similar to voltage sags but extend over one minute.
In mines, the underlying causes of sags and undervoltage may include the start-up of high-power motors, transformer inrush, ground faults, short circuits, or tripping and reclosing circuit breakers. Contributing factors may include the long cables commonly used for mobile equipment, and the incorrect specification of transformers.