Both sags and undervoltage may cause nuisance tripping of breakers, equipment malfunction and shutdown, or premature equipment failure. Operation at reduced voltage will increase heating effects at high-resistance connections, elevating the risk of combustion or explosion in classified areas. Signs of these issues include dimmed or flickering lights, poorly operating HVAC units, and motors running hot. PLCs, automation control systems, and computers may lock up or power down, resulting in lost data, increased production costs, and a greater probability of equipment failure.
2. Overvoltage/Swells
Overvoltage and voltage swells are also be known as transients, spikes, or impulses. The control of overvoltages is critical to maintaining mine uptime. An overvoltage condition may occur by accidental contact of equipment with a higher voltage system, or from transient phenomena due to lightning strikes, intermittent ground faults, autotransformer connections, or switching surges. The maximum ratings for cable insulation, transformer windings, relay contactors, and so forth may be temporarily exceeded in these cases. This does not usually result in an immediate breakdown of equipment, but component parts of the electrical system are successively overstressed and weakened by repeated exposure. This leads to premature failures, reduced component life, and mysterious “nuisance trips,” which can occur without apparent reason.1
One of the serious consequences of overvoltage is insulation degradation. Deteriorating insulation jeopardizes the safe operation of the entire mine power system. Weakened or failed insulation can serve as a catalyst for electric faults, power outages, fires, and the explosion of methane and coal dust. Insulation is designed for its safe maximum applied voltage along with a transient overvoltage rating indicating the peak voltage it can withstand. If regularly subjected to above peak voltage, insulation will progressively weaken until it fails, resulting in a line-to-ground or line- to-line fault. Weakened insulation in a portable mining cable represents a safety hazard since the insulation appears to be functional when a lethal potential may exist on its surface.
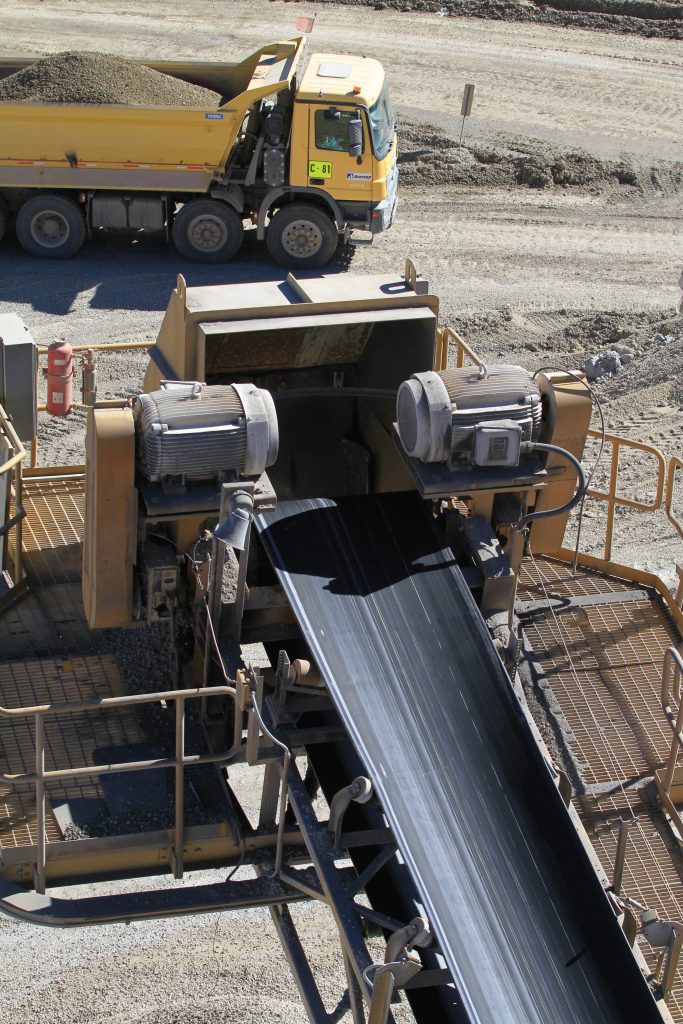
3. Harmonics
Harmonics refer to voltages or currents having frequencies that are integer multiples of the frequency at which the supply system is designed to operate. Harmonics combine with the fundamental voltage or current and produce waveform distortion. Harmonic distortion exists due to the nonlinear characteristics of devices ─ such as Variable Speed Drives (VSD) ─ and loads on the power system (3). Harmonics can lead to increased heating in equipment and conductors, misfiring of VSDs, and torque pulsations in motors. Other symptoms of harmonic distortion in a mining power system are interference in the mine’s communication system, flickering lights, tripped breakers, and even loosened electrical connections.
The vast majority of the loads in a mine are electric motors, most of which today feature non-linear VSDs, making VSDs the main source of harmonics in a mining operation. Standard 3-phase power VSDs have a full wave rectifier that improves motor efficiency but that generates considerable harmonics.
4. Total Power Interruption
In remote areas of the world, local utility grids may struggle with the capacity to reliably support the power demands of a modern mine. Weather can wreak havoc on long suspended power lines supplying a mine. Gensets can fail, as can microgrids, leaving a mine in the dark.
In the event of a total power disruption all mining production comes to a halt. Safety standards require emergency diesel generators to be on- site to supply power to critical loads in case of blackouts, ensuring that mine workers can safely evacuate the mine.
Electrical equipment is another story. If left unprotected, the lifespan for even the most rugged machinery will be shortened as the result of a sudden power interruptions. Blackouts are especially devastating to devices where normal shut down sequences are critical. Sudden power loss for computer-based equipment, such PLCs, automation systems, and industrial robots can result in corrupt files, lost data, and possible damage to the operating systems. When this type of equipment is brought back online, the operating system may fail to boot, or critical operational data may be lost. Furthermore, the physical lifespan of the equipment can be reduced by frequent power losses.
Conclusion
Applying a multi-tier power quality and protection strategy has proven to lower mining costs, minimize hazards, and extend equipment longevity, helping to ensure that operations remain profitable and sustainable over time. Mining equipment has greater power requirements than ever before. These increased and varied loads have come at the same time as the adoption of sensitive electronics in mines for automation. The increased number of devices drawing power from the utility grid has led to greater dependency on the level of power quality required in today’s highly competitive, efficiency-driven mining industry.
- Mine Power Systems, Lloyd A. Morley, January 1990 https://www.cdc.gov/niosh/mining/ works/coversheet624.html https://www.cdc.gov/niosh/mining/ UserFiles/works/pdfs/ic9258.pdf ↩︎