FUNDAMENTAL TO LIFE, clean water is perhaps the most important natural resource on the planet. Unfortunately, with the increasing recurrence of droughts, poor management of resources, and climate change, a scarcity of clean water is reaching crisis status. Four billion people — almost two-thirds of the world’s population — experience severe water shortages for at least one month each year. (1) Even in countries with adequate water resources, water scarcity is not uncommon.
Water scarcity has made the operational reliability of wastewater treatment plants all the more urgent. Wastewater treatment ensures that contaminated water can be safely reused or returned to the water cycle, but never discarded. Wastewater (“sewage”) contains many harmful substances and cannot be discharged into the environment until it is treated. Therefore, the importance of wastewater treatment is twofold: to restore our water supply and to protect us from toxins. Since the Clean Water Act was issued in 1972, more than 15,000 publicly owned wastewater treatment plants (WWTP) have been brought online in the United States, furnishing primary, secondary and tertiary levels of treatment to 34 billion gallons of wastewater each day. (2)
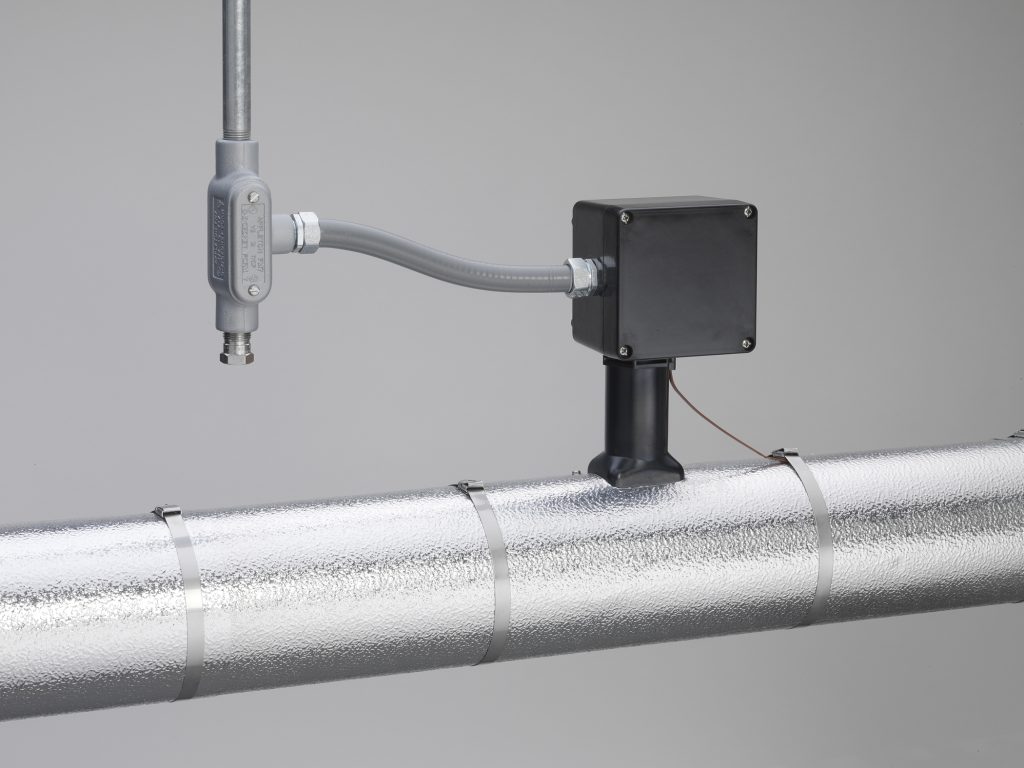
In this article, we address the serious challenges posed to WWTP by cold weather, specifically how freezing temperatures can jeopardize the piping infrastructures that enable plants to convert sewage into clean water. Piping systems are like the veins of a wastewater treatment plant, carrying water, sewage, chemicals, and mixtures from one location to another. Damage to one pipe can lead to a cascading effect onto the entire infrastructure. Unfortunately, the complexity of wastewater treatment systems often means that isolating, repairing, or replacing a single damaged or cracked pipe requires an expensive, time-consuming shutdown of machinery. Thanks to modern-day freeze protection technologies, specifically heat trace cables, WWTP have access to a solution, safeguarding mission-critical pipelines against severe cold weather events.
Winter Weather Challenges
As if the many variables of wastewater treatment aren’t enough to keep a supervising technician busy, winter weather makes the task even more demanding. Snow, ice, and freezing rain can easily create obstacles that will prevent a plant from running at peak performance. Cold temperatures not only slow down the activity of the system’s microorganisms, which do the important work of breaking down contaminants; but it also leads to frozen and cracked pipes, hoses, valves, pumps and process components, as well as ice formation on outside tanks and reservoirs, among other issues.
If left unprotected, just about any machine or component within a WWTP can freeze. Once they do, the plant may need to be partially or completely shut down for repairs. Meanwhile, wastewater will continue building up until the facility restarts, or it may need to be released untreated into a nearby body of water leading to environmental contamination, hefty EPA fines, and bad publicity. A major cause of delays that extend downtime is waiting for vital replacement parts. Generally, these parts are ordered beforehand, however, emergencies like a frozen pipe or valve are rarely anticipated. Besides cracks and flooding, limited freezing of water or vapors in pipes can lead to changes in system conditions that can throw off the ratios of treatment products, rendering them less effective. Not only does this affect system health, but it also greatly reduces efficiency.
The Need for Freeze Protection
An overwhelming two-thirds of capital expenditures for conventional wastewater treatment plants can go toward pipelines and pumping stations to maintain flow. (3) Given this investment, extra measures need to be taken to keep this infrastructure performing at optimal efficiency during the cold weather months
When pipelines freeze in WWTP, the consequences are severe. Leaks and bursts pose a danger to employee health, the environment, and the plant’s financial and reputational status. A recent example is the historic 2021 winter storm in Texas. The brutal cold engulfed vast swaths of the Southwest, shuttering water treatment centers and hindering repairs. Some of the winter storm damages at Texas plants included broken pipes, valves, basins, and impacts to chemical feed systems. This led to service disruptions for water systems in more than 140 counties across Texas, affecting some 14.9 million people at its peak.
Heat Trace Cable
To ensure that wastewater treatment pipelines can operate during the winter, freeze protection needs to be applied. Electric heat trace cables play a major role, offering reliable, safe, and energy-efficient performance.
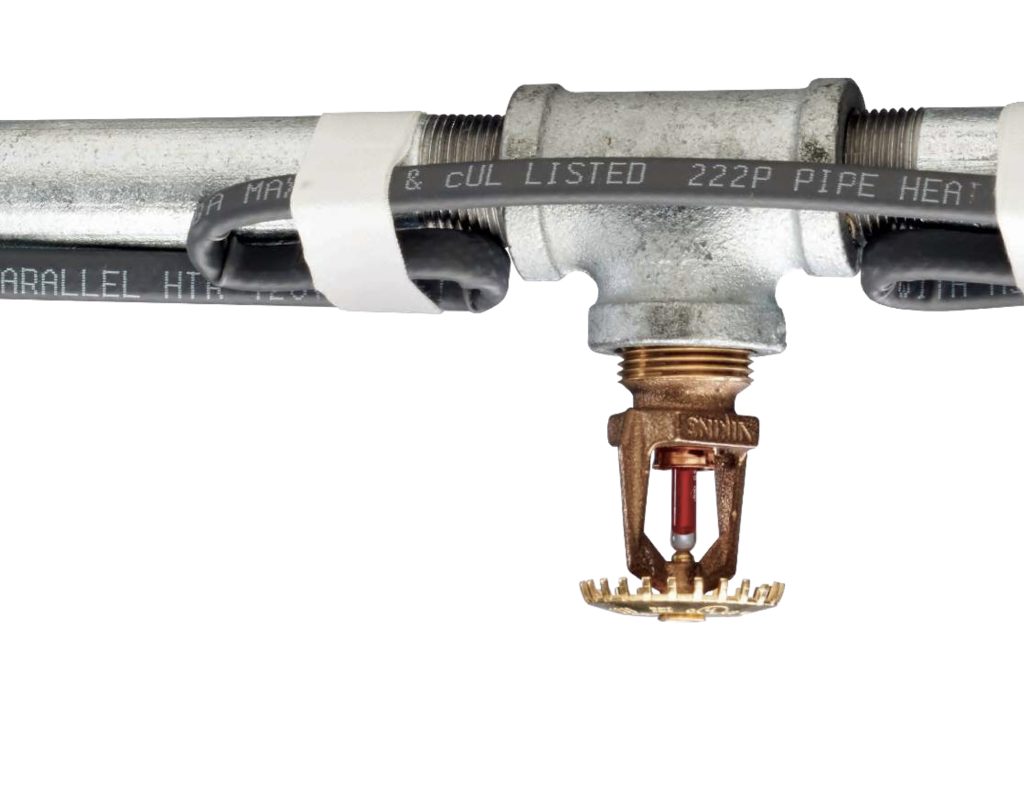
Heat tracing cables are designed to prevent pipes from freezing by use of a resistive element that heats up when electricity passes through it. Replacing lost heat allows the pipe and water/liquids inside to be kept at a constant temperature. If self-regulating, heat output is managed by the ambient temperature. This means that the heater cable will automatically alter the heat output in response to temperature changes across the pipe; it will increase the heat output as areas of the pipe cool, a decrease heat output in areas where the temperature is rising.
Areas of a WWTP requiring heat tracing include the headworks, supply pump stations, influent lift stations, filtration systems, and chemical feed systems (if located outside). Additional areas that should be considered are stairs/walkways, loading docks, and platforms to ensure employee safety. Faucets and washdown areas may also require heat tracing if exposed to the cold temperatures. However, areas such as reactors and digestor systems have enough mass to prevent freezing without additional protection.
When you are specifying a heat trace cable, it is important to establish parameters. These parameters are determined by pipe sizes, lengths, material, number of valves and pumps attached to the pipes, and the type of pipe supports. Other factors are the supply voltage (110/120 Vac or 208/240 Vac), weather data for the area, and the minimum start-up temperature.
WWTP produce flammable gases and vapors. These emissions come mainly from substances that the wastewater could be carrying, such as oils, solvents, or gasoline from accidental spills, and from anaerobic digestion of organic matter. In confined spaces, a high concentration of these gases can build up making the area particularly suspectable to an explosion from an electrical arc. NFPA 820-2020 (Standard for Fire Protection in Wastewater Treatment and Collection Facilities) determined that most pumping stations, spaces, and buildings that make up a WWTP must be considered hazardous locations. In North America, the heat trace cable you specify should be rated for hazardous locations as defined by the National Electrical Code (Article 500), which is broken down into Class, Division, Group, and Zone based on their explosive concentration probabilities. When choosing a heat tracing cable solution for wastewater applications in Europe, ensure it is certified to ATEX, IECEx, CENELEC, EU or other regional hazardous location standards for both metal and non-metal pipes, tanks, and vessels.