YOU DON’T THINK TWICE ABOUT INSURING YOUR CAR, health, and home but what about providing protection for your facilities automation equipment, sensors, servers and microprocessor-based controls and systems? All those are subject to power quality disturbances that cost American manufacturers $26 billion annually in damaged machinery, work stoppage, lost data, and energy costs. The good news is understanding the causes allows you to take some simple steps help manage the problems.
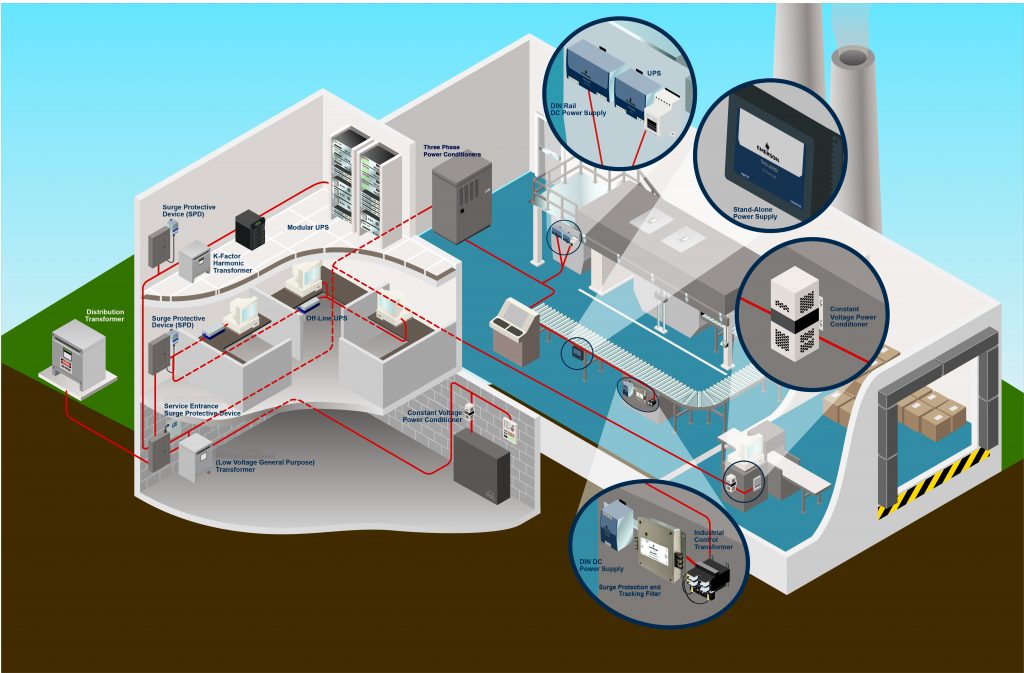
When designing a power system for load sensitive equipment, the main rule is to make power quality the first consideration, not the last. Threats to load sensitive equipment come from inside and outside the facility. These can range from impulses, voltage sags, swells and noise, to interruptions due to utility brownouts and total blackouts. This whitepaper addresses ways to protect against those threats.
Some Sources of Power Disturbances
Outside the facility, disturbances account for approximately twenty percent of recorded power quality events. Along with utility brownouts and blackouts, lightning strikes create high energy, transient voltage spikes that can disrupt power. Don’t forget the utility power factor correction capacitors can cause problems as well. As will re-closures when the utility is clearing faults or switching power. Add in mother nature, high winds that blow tree branches into power lines or ice storms that can bring AC lines into contact with the ground or cause a short between phases. External sources of power quality problems exist everywhere.
Internally, on the other side of the electrical meter is your facility. Eighty percent of power problems are due to issues from inside your own walls. In an average factory, power problems primarily involve surges (62%) and sags (29%), with the balance being impulses, harmonics and the loss of AC line voltage altogether. Culprits may be electrical noise from a variable frequency drive, or a high inrush current from a motor or spot welder, or an electric arc furnace drawing several times its full load current when starting. Add to that other factors that can threaten power, improper grounding, improper routing, or even an undersized distribution panel. Whatever the source, poor power quality jeopardizes machine availability and ultimately, profits.
Throughout your facility, there exists mission-critical equipment, each interdependent on one other, complicating your electrical system. Power quality problems can bring any one of these operations or controls to a grinding halt at any time, usually at the worst possible moment. Power quality disturbances occur at varying magnitudes and rates, depending on the utility power at the service entrance and the electrical/power infrastructure on the plant floor. Plus, different types of equipment are sensitive to different types of loads. Microprocessors are highly sensitive to impulses, like motors or HVAC compressors. Lighting systems are susceptible to sags, swells or brownouts. Computer based controls, data storage, alarms and safety equipment are easily damaged by power interruptions. The truth is, even the most ideally installed and maintained equipment in a perfectly engineered facility can introduce power quality problems as the equipment ages.
To keep your facility up and running efficiently, you need to determine the costs of prevention and remediation, and then compare those to the costs of poor power quality interrupting or damaging your facility or systems usually resulting in downtime and lost productivity.
Total Power Quality Solutions
You need to understand and implement a means to stabilize, control and manage your power equipment needs — from the service entrance down through the branch distribution panels, including all critical points of use, as well as controls, communications and data lines. You need a comprehensive Total Power Quality Solution.
Control Power Solutions for Point of Use
To prevent premature wear on machines and computer equipment, you also need to protect them from momentary losses of line voltage, which are the most frequent of power quality disturbances found in industrial facilities. You need to enable your electrical system to safeguard almost any equipment application with a complete line of switching and linear power supply technologies. Properly sized power supplies ensure the right voltages are getting to your equipment or controls, regardless of voltage sags.
Control transformers are installed to convert the available voltage to accommodate electrical circuit or equipment requirements. They are designed and built in a vast range of configurations to meet requirements for variables such as power, heat, voltage and environmental conditions.
Power Quality Solutions
Protecting critical data on network devices from surges and noise is critical to production. Adding surge protection devices is an essential line of defense in protecting your production line and facility. They focus on limiting high-voltage spikes to a level that is acceptable to most electronic equipment. Choose components that are placed in parallel with the line and serve as a clamping mechanism for high-energy impulses. Tracking filters are an ideal solution for microprocessor-based products to provide clean AC power at the equipment level avoiding damaging degradation or “electronic rust” over time. Finally, data/signal line products can be used to protect your point of use equipment from high-energy impulses protecting controls and critical data you need for your operation.
One of the most effective means for optimizing and protecting production efficiencies is with dedicated power conditioning solution. Power conditioners insulate equipment from damaging transients and noise, voltage surges, harmonics and changing voltage conditions that cause 95% of all power quality issues, except a total loss of power.
Because you cannot always control a complete power loss, uninterruptible power supplies (UPS) can be installed alternatively to ensure continuous operation and/or data protection during a power interruption. Certain UPS prevents power interruptions from affecting production and seamlessly switching to back-up battery power the instant it detects a voltage irregularity.
Power Distribution Solutions
Reliably converting the voltage coming into facilities is essential. Facilities are challenged in procuring the transformer that can safely, efficiently, and reliably deliver the proper voltage for their specific needs. There are a broad range of transformers available for applications across manufacturing facilities, most can be manufactured standard or depending on the application specifically configured for your needs. This means they are designed and built to meet requirements from normal to harsh environments with power, heat, voltage, and environmental conditions in mind.