INDUSTRIAL-GRADE LED LIGHTING LUMINAIRES are exposed to some of the toughest environments on earth — from the deserts of Saudi Arabia to offshore platforms, to the North Slope of Alaska. Many of these environments are hazardous, and dependable lighting is essential to keeping workers safe.
Reliable LED lighting is key to improving operational efficiency and reducing expensive maintenance costs. Reliability begins with a rigorous process, where the electrical engineer or facilities manager must qualify which designs perform in environments relative to corrosive atmospheres, extreme temperatures, heavy vibration, and electrical disturbances. In this article, we address these essential qualities and other critical factors
in specifying industrial-grade LED luminaires.
Corrosion Resistance
Exposure to caustic chemicals and solvents, adverse weather, salt water and moisture will corrode unprotected luminaires and lead to premature failure. Therefore, it is important to understand the finishing processes a manufacturer applies to protect their luminaires from the surrounding corrosive environment. Various finishes can be applied to help isolate metallic surfaces from the surrounding corrosive environment. The most familiar example is ordinary paint applied to steel to prevent rust.
However, there are several other methods including baked enamel, epoxy powder coat and PVC coating. For effective protection, coatings must be applied properly and protected against damage during installation and use. Unlike liquid paint, powder coating uses an electrostatic process to apply a finish to metallic parts in a dry state. Once applied, the finish is heat-cured to create a finish that is thicker, tougher, more even on all outer surfaces and edges, and more durable than most paints. This makes epoxy powder coat one of the preferred protection choices for oil and gas, wastewater and other harsh, corrosive industrial applications.
Gasket Protection
Industrial-grade LED luminaires have gaskets that keep water and dust on the outside. Critical to reliability, those gasket seals should be tested to the stringent application requirements encountered in heavy industrial and hazardous applications. Gasket performance testing is conducted according to ASTM-D-395 through ISO accredited third party laboratories. For example, aging tests should include thermal endurance spanning -50°C to +120°C (-58°F
to +248°F), humidity levels of 95% RH, and continuous Ultraviolet (UV) exposure. Top grade gasket material is composed of high-performance closed cell silicone foam. The superior low compression set characteristics deliver years of reliable service in the toughest environments on the planet.
Dust Accumulation
Dust is an especially destructive agent to LED luminaires. In addition to accelerating corrosion, dust can prevent heat from escaping, cause conductivity issues and retain moisture. Dust often contains oils, minerals, chemicals and other materials that can diminish the reliability and life span of the luminaire. To combat dust, industrial-grade LED luminaires must be designed to be IP6x Dust Tight. A superior protective coating will help prevent dust from corroding luminaires, while silicone gaskets will seal out dust particles from sensitive electronics. Another approach is to utilize vertical radiating surfaces – such as fins – to let the dust fall through rather than build up on the luminaire’s heat dissipation surfaces.
Thermal Design
LED reliability begins with good thermal design. Industrial LED luminaires must emphasize thermal performance first and foremost to provide long term field reliability. Extensive thermal simulation during the design process should be performed on the luminaire to ensure driver electronics and LED semiconductor devices operate within their thermal limits even at the fixture’s maximum rated ambient temperature. Also, no failure prone fans or other active thermal management devices should be employed. Instead, the design must optimize housing thermal conduction, maximize radiating surface areas, and employ strategically placed thermal conduction breaks to balance heat flows.
Shock and Vibration
Industrial-grade LED lighting fixtures are designed to be used in areas where high vibration is a constant occurrence. Vibration from heavy machinery and processing equipment can disengage fixtures from mountings, endangering employees and causing lighting failures. While LEDs generate light using solid state engineering, the wires and connections in low-quality fixtures can loosen from extended vibration. Exterior features, such as captive hardware and integral redundant die cast safety retention points, will help protect workers from parts falling into work areas and production processes. Vibration tests for LED luminaires involve sweeping through a range of frequencies and resonance points in the x, y and z axis with Gs well beyond expected application levels. To ensure interior components remain protected, impact tests are performed to IEC and NEC/CEC standards after material aging and temperature cycling to verify robust enclosure performance.
Surge Suppression
Abnormalities in electrical signals can lead to lighting irregularities such as flashing, strobing, flickering, loss
of brightness and premature luminaire failure. The most common electrical signal disturbances are voltage surges, also known as transients. Lightning strikes and electrical devices such as motors and circuit contactors can induce transient surges that pose a threat to LED lighting installations. Industrial-grade LED luminaires should include a robust 6KV surge suppression circuit to protect against damage caused by surge energy, therefore enhancing reliability, minimizing maintenance and downtime, and extending the life of the lighting installation. In high surge risk areas look for luminaires offering 10KVs urge protection.
High Quality Illumination
A key value of LED lighting is in enabling employees to comfortably and safely work in harsh industrial or hazardous environments without the challenges of bad color, shadows, glare, and inconsistent illumination. Below we explain the qualities that ensure high-quality illumination in an industrial-grade LED luminaire: secondary optics, beam pattern, color temperatures and lumen level.
Secondary Optics
A high-quality LED luminaire maximizes usable light appropriate for the application. Secondary optics are used to direct light from the source to where it is needed. Unlike HID lamps, LEDs are highly directional, requiring specialized optics to reduce glare and provide even light distribution in a beam shape optimized for specific applications. Well-designed optics can help designers achieve ideal spacing and minimize the number of luminaires required.
Beam Pattern
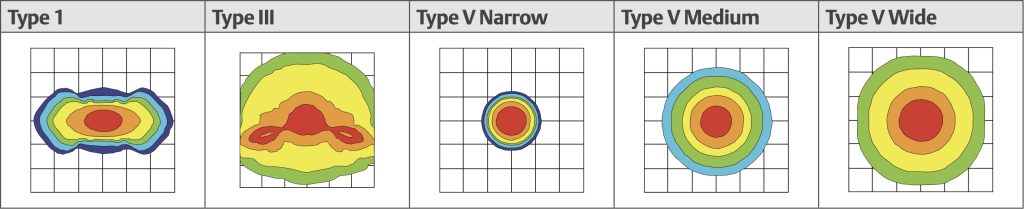
The Illuminating Engineering Society of North America (IESNA), specifies different types of luminaire light distribution classifications for roadway lighting. Besides roadway lighting, they are also commonly used to describe the distribution of fixtures installed in industrial and hazardous applications for task, area, low bay and high bay lighting applications.