While some of these effects could be dismissed as no more than irritants, others such as process equipment failures, can lead to costly downtime. Worst of all are failures of electrical distribution equipment like cables, transformers, motors and standby generators.
Here the replacement equipment is likely to be expensive and today, may only be available on a long lead time. In these cases, both the repair costs and the resulting costs can be substantial. Even if there are no outright failures, the presence of harmonics will cause reduced electrical efficiency within the installation leading to excessive power consumption which you will be paying for.
Eddy current heating in motors and transformers is proportional to the square of the harmonic frequency, so it follows that as the presence of higher order harmonics in the supply system increases, the heating effect will increase even more dramatically. Not only does the generation of heat waste energy – which you are paying for – it also increases the risk of failures of or even fires in wiring, motors, transformers and other distribution equipment.
In addition to the losses that result from heating effects, harmonics in motors can give rise to torsional oscillation of the motor shaft. Torque in AC motors is produced by the interaction between the air gap magnetic field and induced currents in the rotor. When a motor is supplied non-sinusoidal voltages and currents, the air gap magnetic fields and the rotor currents will unavoidably contain harmonic frequency components.
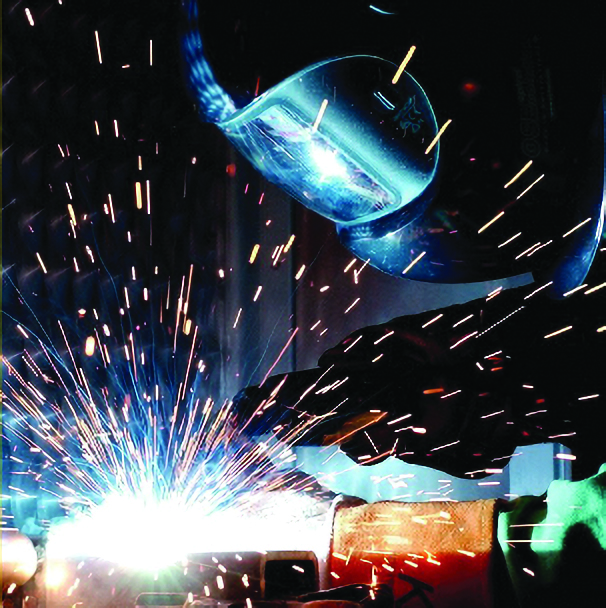
+ Sequencing | 1, 4, 7, 10, 13 |
– Sequencing | 2, 5, 8, 11, 14 |
Zero Sequencing | 3, 9, 15, 21 |
These are grouped into positive, negative and zero sequence components. Positive sequence harmonics (1, 4, 7, 10, 13, etc.) produce magnetic fields, and hence torque, rotating in the same direction as the field and torque produced by the fundamental frequency of the supply. Negative sequence harmonics (2, 5, 8, 11, 14, etc.) produce magnetic fields and torque that rotate in the opposite direction. Zero sequence harmonics (3, 9, 15, 21, etc.) do not develop torque, but produce additional losses in the machine.
The interaction between the positive and negative sequence magnetic fields and currents produces the torsional oscillations of the motor shaft, which appears as shaft vibrations. If the frequency of these vibrations coincides with the natural mechanical frequency of the shaft, they become amplified and severe damage to the motor shaft may occur.
Some of the most troublesome harmonics are the 3rd, and odd multiples of the 3rd, i.e. the 9th, 15th etc. called “triplens”. The triplen harmonics on each of the supply phases are in phase with each other so they add rather than cancel in the neutral conductor of a three-phase four-wire system. This can overload the neutral conductor if it has not been sized to allow for the potential presence of harmonics.
While the harmonics usually cannot be removed, since they are generated in the course of the normal operation, they can be prevented from spreading throughout the distribution system.
This is usually done by installing passive or active filtering close to the source of the harmonics, and in some cases, by the use of tuned power factor correction equipment. Bringing harmonics under control will eliminate, or at least mitigate, all of the problems we have discussed.
A note of caution is needed. Adopting measures to alleviate harmonics is unlikely to be a once-and-done solution. In today’s changing business environment, it’s likely that new loads will be connected to your electrical installation. Without measuring, you won’t know how these are affecting overall harmonic performance? Therefore, regular monitoring of harmonics is strongly recommended if the benefits of harmonic reduction are to be maintained.
Sags and Surges
If electrical equipment is to operate correctly, it requires electrical energy to be supplied at a voltage (and frequency) that is within a specified range.
In practice, what really matters is it compatible with the loads that are connected to that supply. Sometimes this is not the case, mostly due to voltage sags and surges.
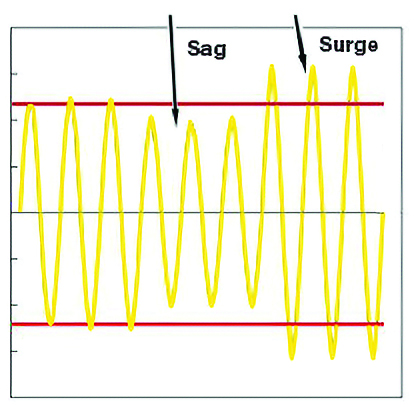
What are voltage sags and surges?
A voltage sag is a sudden reduction in the supply voltage of between 10% and 90%, which typically lasts between 10 ms and 1 minute. The depth of a voltage sag is defined as the difference between the minimum RMS voltage during the sag and the declared supply voltage. Voltage changes that reduce the supply voltage by less than 10% are not considered to be sags.
Voltage sags may be caused by external factors on the supply or internal factors within an installation.
They can be single events that occur at random, or a series of events that repeat in some pattern. In all instances, monitoring and recording the supply voltage over time will show exactly what is happening and help to locate the cause.
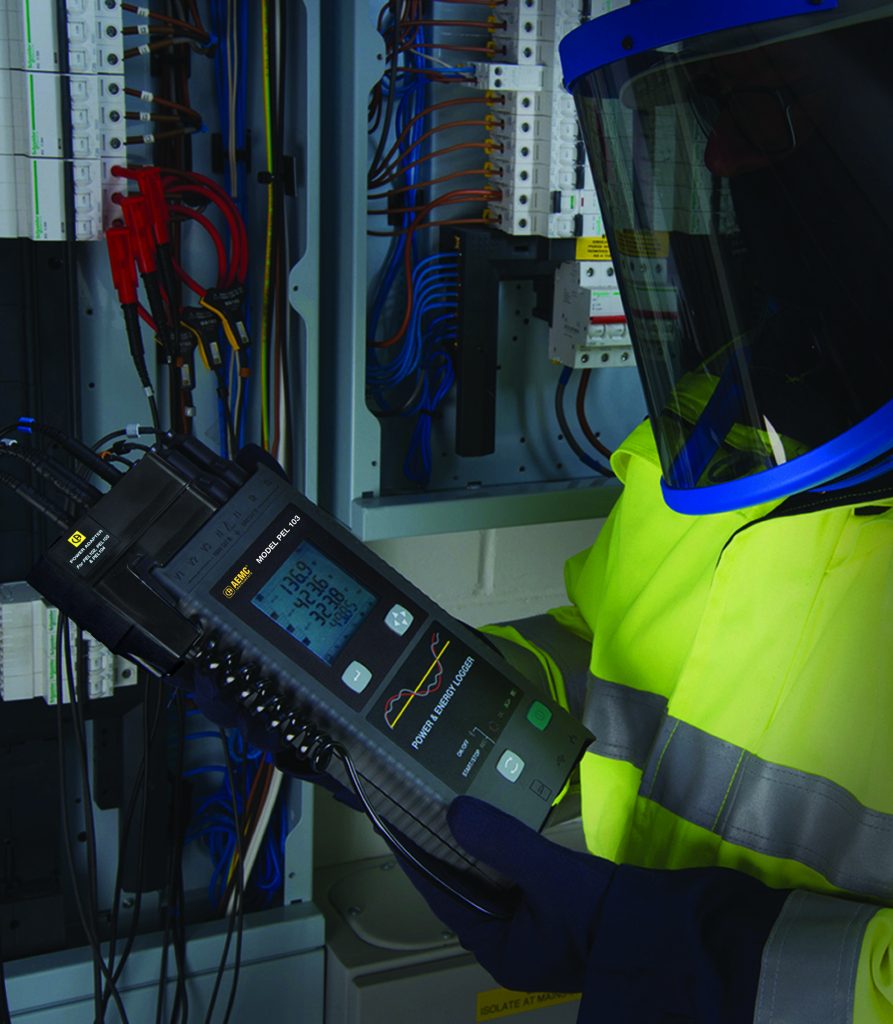
External factors are more likely to produce single events and include load switching and fault clearance in the supply network. A similar effect can occur when switching between the line supply and uninterruptible power supplies or emergency back-up generators. Common causes of voltage sags within an installation are the switching of large loads, such as motors, arc furnaces and welding equipment, and the operation of loads with fluctuating current demands. Often voltage sags produced within an installation occur at regular intervals or at particular times.
The effect that sags have on electrical equipment and building occupants varies widely and is dependent on the kind of event and the type of equipment connected to the supply system.
Supply voltage sags can cause particular problems, with varying degrees of severity, for AC induction motors. As the supply voltage to the motor decreases, its speed tends to decrease. Depending on the depth and the duration of the voltage sag, the motor may return to its normal speed when the supply voltage recovers. If the magnitude of the sag or its duration exceed certain limits, however, the motor may stall, or it may be disconnected from the supply by a contractor dropping out or the operation of an under- voltage trip.